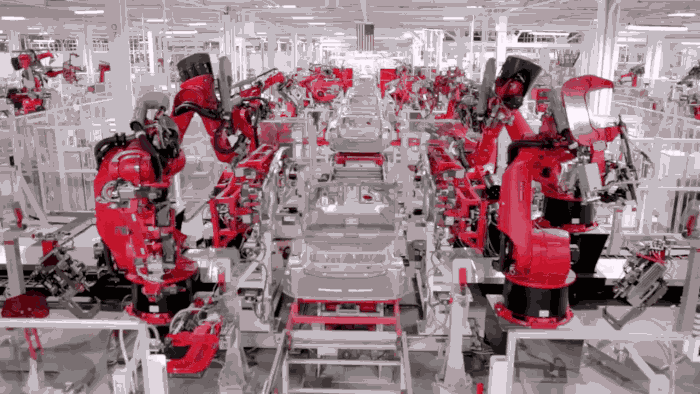
In manufacturing terms, ‘just-in-time‘ is an approach where you try and hold as little stock or spare inventory as possible. Ideally, you want a part to turn up ‘just-in-time’ for it to be added to the car as the car rolls down the production line (just-in-time manufacturing was pioneered by Toyota). Because holding spare inventory comes with costs (you have to pay for it before you need it, you have to store it and you have to double handle it), ‘just-in-time’ is generally seen as a desirable approach and one that’s synonymous with being an operation being productive and ‘lean’.
The only problem with just-in-time is when things go wrong. Without any spare inventory, the production line stops and nothing can happen until the required parts turn up (apparently, Ford currently has over 22,000 partly built cars waiting for parts). When things go wrong, you would very much wish that you didn’t follow a ‘just-in-time’ strategy and instead you’d gone for ‘just-in-case’. As the name suggests, a just-in-case strategy means that you intentionally leave some excess capacity in the system, just in case things go wrong.
But the concepts of just-in-time and just-in-case don’t just apply to manufacturing; they apply…everywhere. Over the last two years, it’s become prudent to have a just-in-case toilet paper strategy, a just-in-case home office setup and (more recently) a just-in-case collection of RAT tests.
Another way of framing this is,
“In times of clarity and predictability pursue productivity,
but when the shit hits the fan, have backup plans.”*
*thankfully I’m a better futurist than poet
And between global pandemics, regional wars and local flooding, there’s little doubt that we are currently operating in times of heightened uncertainty. The time for making a plan (singular) has passed, it’s now time to be making plans (plural). As the Chaser points out in this recent tweet, having just one plan is no longer a sound strategy.
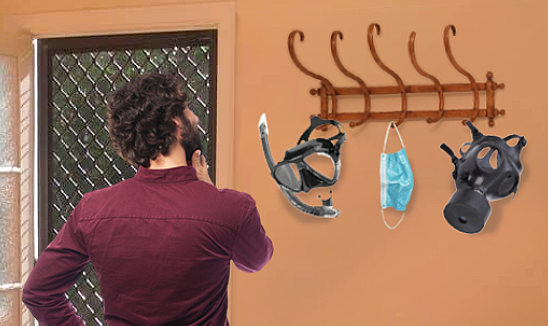
— The Chaser (@chaser) March 1, 2022 https://pic.twitter.com/93mTJkIU6J
In his book ‘How to Lead a Quest‘, my good mate, the wizard, rogue, scholar Dr Jason Fox describes this as having a ‘quiver of options’. By investing in a selection of pre-considered and validated strategies now, you pull them out and fire them off when the moment is right.
The irony is, although right now is the best time to have a quiver of options, it also feels like the hardest time to develop them. Let’s be honest, doing good strategic planning when times are stable and predictable feels hard enough. Doing it when the environment is changing rapidly and it’s unclear what to plan for, feels nearly impossible. It’s human instinct to sit on the sidelines, conserve energy and hope for clarity…
…but as they say, hope is not a strategy.